In the increasing development on battery-powered products, such as energy saving and electric vehicle, it’s very essential to verify the durable and safe performance of these electric systems. In terms of battery, we can divide them as three types according to size. The smallest is battery cell. It’s also called as a single cell. We can often find it in our life like 18650 and 21700 cylinder type. Then, when several cells are integrated together by series parallel form, this new one is a battery module. Normally, it is used in electric motor car and electric bicycle. Finally, when several module are combined together, it will become a battery pack which can be seen in electric bus, stationary applications and light electric rail (LER) applications. Various types of samples use various corresponding standards. So today, this aritcle is to discuss main differences in testing object and purpose. Besides, we will explore how to select a suitable solution for your battery specimen. Because if the users lacks of the awareness of rigorous and thorough test, it will have consequence to safe risks, lower performance or system failures. The even worst situation is money and time will be wasted, and then users won’t get the accurate test data accordingly.
Understanding the Test Object of Each Standard
When it comes to this point, I have met some of customers who didn’t know to use which standard to test their batteries. The most ridiculous things is they often ask cell test equipment based on ECE R100 and I have to explain it to them every time. Thus, it’s important to know the test obejct of each standard.
1) If you test battery cell, then UN38.3 is the best. It has tests like crush, impact, altitude, temperature clcying, external short circuit, vibration, shock, charge and discharge. In addition, UN38.3 is not applicable for testing battery pack because some test conditions between cell and pack is very different can’t use in big pack.
2) If you test battery module in moto electric car, then you can use ECER136. It includes tests such as vibration, thermal shock, drop, mechanical shock, fire resistance, external short circuit and over-charge-and-discharge. Besides, users can also choose ECE R100 to test their modules.
3) If you test battery pack system in electric bus, we advise you to adopt ECE R100. There are tests like crush, fire resistance, thermal shock, external short circuit, vibration and shock.
By figuring out of these, it will greatly help you save much budget and time. In addtion, you don’t need to worry too much whether the equipment you bought works or not.
Choose a Suitable Solution for Your Battery
It’s very important to select an available plan for your battery specimen. I encountered some cases that our customer requested to use one machine for testing their battery cell and battery pack according to UN38.3 and ECE R100 standards. However, not all test conditions are the same in these two standards. Only one test like temperature cycling can achieve that. For the other tests such as crush and external short circuit, their requirements are very different between these two standards.
Reagrding crush test, UN38.3 requires crush force of about 13kN, and ECE R100 is about 100kN. So you might have a question why don’t we want a machine with 100kN? Actually, it can’t because it’s all about force accuracy. If machine is 100kN, then its min force is at least about 15kN which is greater than 13kN already. When this machine starts 1s, then it reaches 15kN right away and very hard to control such small value.
Regarding external short circuit test, UN38.3 has requirement of 80±20mΩ resistance range while ECE R100 requests 5 mΩ. Besides,UN38.3 also requires temperature range of 55. In fact, machine can be intergrated with these parameters. However, it will have a problem of current sampling accuracy. Usually, battery pack requires a large current sensor and cell requests a small current sensor. If machies is customized based on UN38.3 and ECE R100, then it only can use the large current sensor (which has lower sampling accuracy) to collect current. And then, the result will have bigger error than the actual value. In addition, such a customized machine is very in high cost.
So far, BELL has more than 17-year experience in battery safety test equipment and has done plenty of projects before. We have a strong R&D teamand are able to customize different solutions for our customers accordingly. We often provide customers with a full set of equipment and help design layouts for them. Most components are imported from oversea coutries like Japan, Germany, USA and so on.
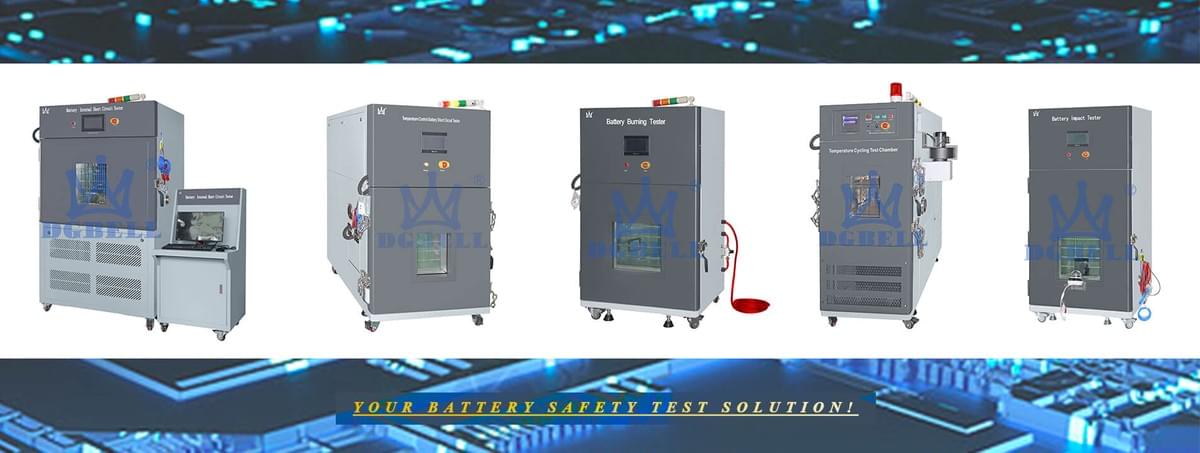
Summary
By reading this airtie, I wish it can help you understand more about battery testing things. Knowing the difference in different test standards, you can choose what you actual need in the following days.